
The Working Principle of Vapor Phase Reflux Vapor phase reflow averts problems resulting from varying PCB components.ģ. To reduce these issues, PCB assemblers and designers opt for vapor phase reflow. The result is uneven heat distribution, which could lead to the warping of the PCBs. That’s because the heat these components store varies significantly depending on their groups.
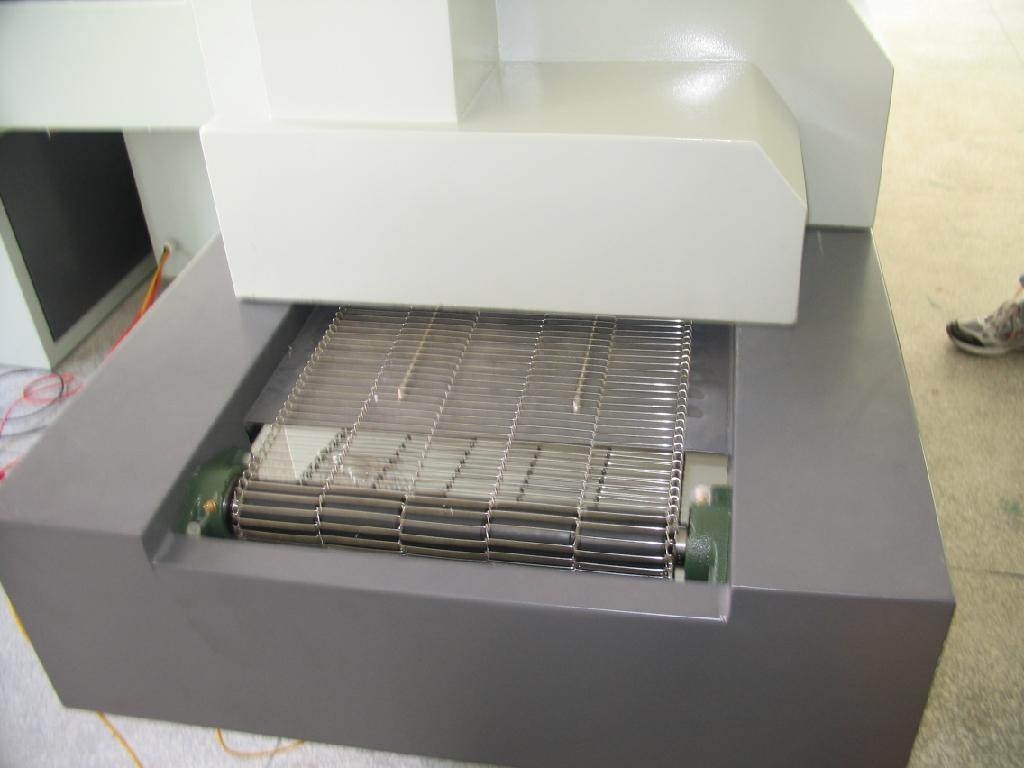
PCB circuits to require parts of different masses, making the soldering process a complicated one. Vapor phase reflow technology helps counter this problem by eliminating temperature fluctuations, topography, and board layout. As a result, the risk of damage to the electronic units due to overheating is higher. These bases need manufacturers to use even higher temperatures to melt the solder effectively. The vast majority of manufacturers now opt for leadless solder bases. There are many reasons for this development. Vapor phase reflow is quickly replacing other soldering technologies in the market. In the end, PCB assemblers get the highest possible PCB soldering results.Īutomated soldering machines are the norm in vapor phase reflow. Moreover, the entire soldering process takes place within an inert atmosphere. This soldering process provides the ideal wetting of the details.

Vapor phase reflow soldering ensures that the PCB board and its members don't face temperatures higher than necessary. It’s a complex process that has become even more challenging as electronic components become smaller. To solder electronic components to PCBs, manufacturers usually need high temperatures. This technology has, in recent years, gained massive popularity among large-scale PCB assemblers. Vapor phase reflow refers to an advanced PCB soldering technology that uses an inert liquid with a high boiling point. This comprehensive guide tells you all you need to know about the vapor phase reflow. Such temperatures might damage the board's structure or the various components. One of the top difficulties PCB designers and PCB manufacturers encounter has to do with the high temperatures of PCB welding.

Over the years, large-scale PCB applications have faced significant challenges due to the soldering process.
